Motivation
Laser-induced plasma micromachining (LIPMM) is a novel tool-less process that has the potential to achieve high material removal rates on materials such as aluminum, transparent ceramics, silicon wafers and polymers. LIPMM can reduce machining time up to tenfold and can overcome the limitations of other conventional micromachining processes. LIPMM also has a wide variety of applications, including semiconductors, micro-electronics, hydrophobic surfaces, and biomedical structures such as bio-absorbable poly-L-lactic acid (PLLA) stents.
Description
Fig. 1: Schematic of LIPMM process, and close-up image of laser induced plasma
In LIPMM, a focused, ultrashort pulsed laser beam creates a highly localized plasma zone within a transparent liquid dielectric, such as distilled water or kerosene. The workpiece is also submerged in the dielectric. When the beam intensity is greater than the irradiation threshold in the dielectric media, plasma is formed and ablates features on the workpiece. Current investigation and challenges include optical, magnetic and chemical manipulation in the process and the control of feature geometry. More specifically, an external magnetic field influences the induced plasma in intensity, shape and size, which increases process flexibility.
Approach
One aim of this research is to develop models of the multi-physics based plasma-workpiece interaction during the process which incorporate beam propagation, plasma formation, and optical enhancement. These models will be validated with experimental work on a wide variety of materials. In particular, one part of this project is investigating magnetically-assisted LIPMM utilizing external magnetic fields that surround the workpiece and machine channel geometries with optimal aspect ratios, material removal rates and heat-affected zone areas. Varying the orientation of the external magnetic field in respect to the plasma plume will change the intensity of the plume and the geometry of the resulting textured channel, as seen in Figure 6.
Fig. 2: Time-series images of laser induced plasma in steps of 16 ps, captured by ultra-fast gated camera |
Fig. 3: Plasma fluence as a function of time, captured by ultra-fast gated camera |
Fig. 4: Poly-imide (M. P. 249 deg. C) machined by (left) LIPMM, and (right) laser ablation, showing significant reduction in heat affected distortion with the LIPMM process ![]() |
Fig. 5. Orthogonal configurations of uni-directional magnetic fields at plasma plume: (a) longitudinally up, (b) longitudinally down, and (c) transverse; (d) Signal count vs. delay plots corresponding to configurations ![]() |
Fig. 6. Typical micro-channel cross-sections made by LIPMM in the presence of magnetic fields directed (a) longitudinally upwards), (b) longitudinally downwards, (c) transverse, and (d) no magnetic field
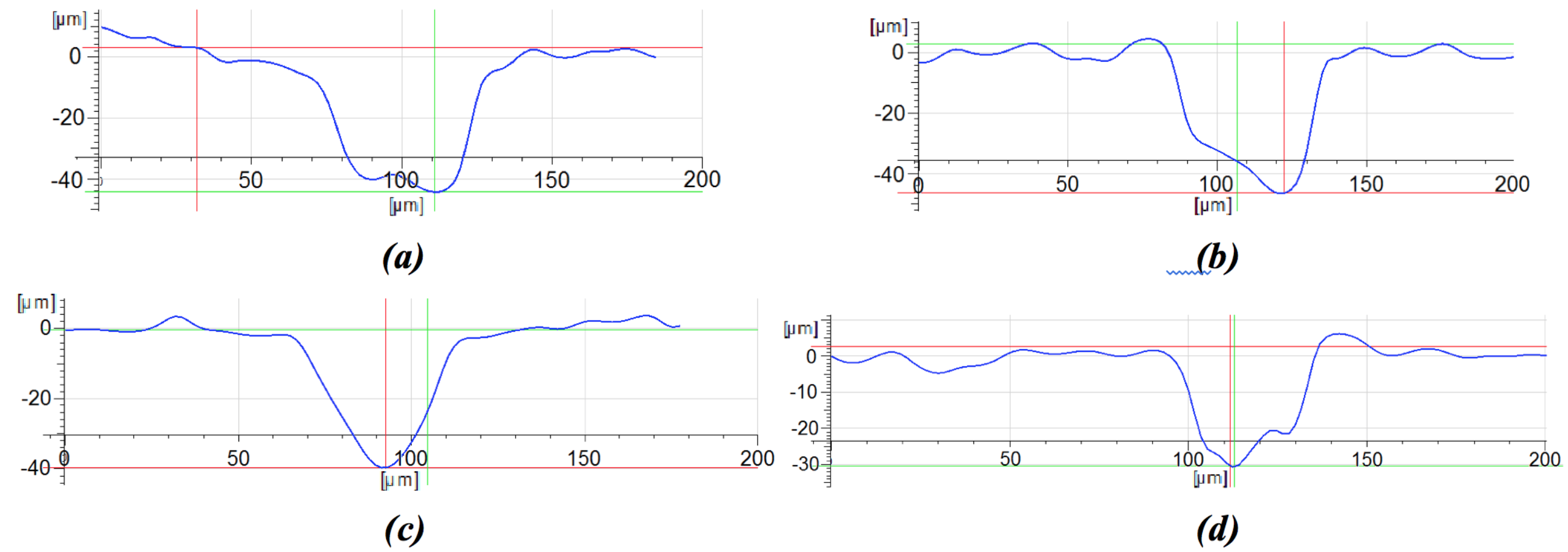
Sponsor
National Science Foundation (CMMI-1335014)